Application 101: Radiators
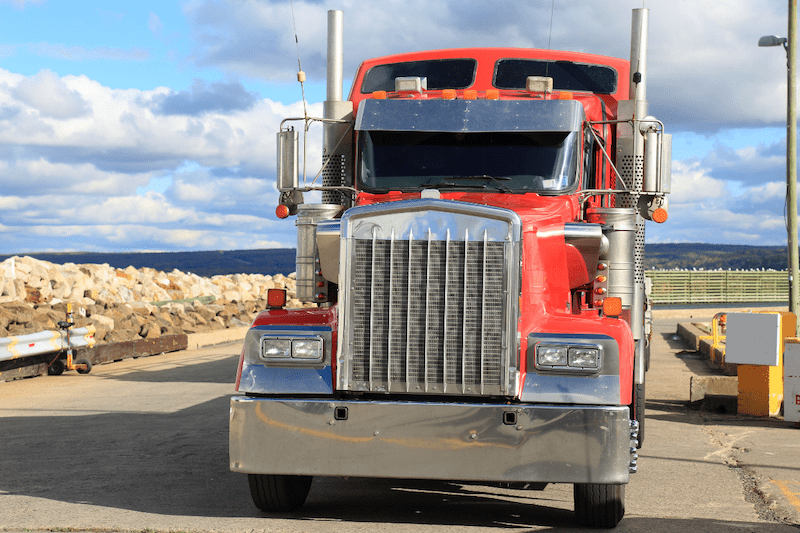
Engine Cooling Radiators - An Overview
We hate to break it to you, but a radiator is not really a radiator. In the same way that a guinea pig is not a pig, tin foil is actually aluminum, and your funny bone is in fact a nerve, a radiator does not radiate heat.
Radiators found in vehicles, building HVAC, and similar heating and cooling equipment dispel heat by convection, not radiation, but after nearly two hundred years of being called by this misnomer, we’re not likely to set the record straight with this single blog post. What we can do, however, is explain how these convective heat exchangers – we mean radiators – work in engine cooling applications, as well as what key considerations come into play in radiator-cooled systems.
Though there is some debate as to the original inventor of the radiator, we know that the concept dates back to the early 19th century and was primarily intended for heating human-occupied buildings.
Radiators consist of metal tube arrays that carry a hot fluid internally, where that fluid transfers its heat energy into the airspace around it, cooling the internal fluid and heating the external air space.
The original goal of radiators was to drive heat ‘into’ the ambient environment, whereas engine radiators have the opposite goal using the same thermal principle – to extract heat ‘out of’ the internal fluid into the ambient environment. In modern use, radiators use low-density, highly conductive materials with added heat sink fins to provide large, efficient surface areas through which thermal energy can be dissipated from internal fluids to ambient air, often with powered fans driving airflow across the radiator to aid in this heat transfer.
Engine Cooling Radiator Applications
Cooling radiators are used anywhere that a hot fluid needs to dissipate heat into the ambient atmosphere at a faster rate than could occur naturally through the surface of the equipment being cooled. There are countless applications for this type of cooling, so to keep this list of examples relatively short, let’s fit all engine-driven applications into one of three categories:
- Vehicle Engines – practically every internal combustion engine in automobiles, aircraft, motorcycles, tractors, freight trucks, and so on utilizes a radiator to expel heat from the engine’s coolant. Even some spacecraft and seafaring vessels use radiators!
- Fixed Equipment – stationary equipment powered by fuel-driven engines include large generators, mining conveyors, irrigation pumps, material elevators, and essentially anything else requiring a large workload to be performed and where electrical or other power sources are not suitable.
- Mobile Equipment – smaller versions of the above items can be found in mobile varieties, such as tow-behind generators, air compressors, water filtration systems, and all sorts of emergency response gear. Here again, fuel-driven engines that require radiators can serve any and all equipment where mobility and self-contained energy sources are desired.
Engine radiators inherently have only one goal: that is, to remove waste heat from an engine in order to maintain a lower operating temperature, which in turn promotes higher performance, lower wear, and longer life. Interestingly, new modern concerns in sustainability and energy conservation have introduced another potential application for radiators known as energy reuse or regeneration.
Commonly found in industrial engineering, energy reuse is the process of taking waste energy from one source and using it productively as input elsewhere in the system in place of consuming fresh raw energy. We can get a sense of this theory in our vehicles, where waste engine heat is used to warm the interior cabin using a heat exchanger, but this isn’t technically a reuse situation as we’re not alleviating consumption of other fuels.
A true, comparative example can be found in this recent project of ours: an agricultural client using diesel irrigation pumps wanted to install a remote radiator in their seed shed where the pump engine’s waste heat could be used to keep the seeds warm in place of turning on a separate gas-fired furnace. Unique applications such as this help to tap into waste energy that would otherwise have been vented into the atmosphere, and are great ways that radiators can put their waste heat to productive use.
Key Considerations in Selecting a Vehicle Radiator
Manufacturers of radiators have gone through a multitude of designs since their invention, finding some designs to be best suited for building heating applications, and others best suited for engine cooling applications. While these design groups are not interchangeable and do not visually appear similar, we do encourage readers to make sure they’re referring to engine or vehicle cooling radiators when chasing down their options just in case.
In the vehicle radiator family, two common designs can be found:
- Bar and Plate. This configuration consists of many fluid channels installed straight between supply and discharge tanks in a common frame, splitting coolant flow down these channels. Thin sheet metal fins are attached between channels, which help to draw heat out of the coolant by adding surface area exposed to ambient air. Airflow is generated by vehicle motion as well as its radiator fan, which then flows directly across channels and immediately removes heat from the coolant within. This design balances cost and features, and offers multiple options in fin configurations that can enhance thermal efficiency and engine performance.
- Tube and Fin - is the default design for vehicle radiators and are quite similar in concept to the above Bar and Plate style but have one key difference: the coolant channels are configured in continuous, serpentine patterns which expose coolant to much longer paths of travel against incoming airflow. This increased channel length increases the potential amount of heat that can be dispelled into the air, offering higher thermal efficiency and performance. While higher heat loss is the goal of this style radiator, realizing this goal is difficult due to having more variables, higher pressure losses, and more fins that can become damaged in normal use. For these reasons, serpentine style radiators are typically only used in competitive sport or max-performance applications.
As a vehicle cooling radiator manufacturer, the vast majority of radiator units we ship are Plate and Fin style due to their simplicity, reliability, competitive cost, and ease of maintenance. To make sure that our units live up to their design potential and keep our clients on the road, we include the below features on all Cincinnati Radiator units as standard options, which exceed the requirements of most vehicular applications.
- Technical Design: any Radiator purchase discussion should begin with full engineering specifications on the engine, cooling load, and operating conditions that make up the application, which will drive the selection of the correct unit to begin with.
- Construction: bar and plate construction is the most preferred style, selected for its very simple assembly and easy repair should there ever be a problem.
- Materials: all-aluminum materials offer the best combination of low weight, high thermal transfer, and economical cost.
- Cleaning: both pre-and post-brazing, Vehicle Radiators should receive a thorough cleaning pass inside and outside of the unit to ensure proper fabrication and in-vehicle performance.
- Assembly: Vehicle Radiators are engineered for a specific heat transfer target based on airflow, surface area, and temperature delta, which means that each Radiator should be assembled to very exact dimensions and tolerances in order to achieve the expected design point.
- Brazing: brazing connections using high-alloy aluminum with additional sheet cladding achieve deeper penetration, which helps combat leaks even under aggressive conditions over many years.
- QC: to assure that the assembly process was a complete success, every unit should be fully checked prior to shipment for dimensional accuracy, brazing penetration, joint integrity, and zero leakage.
- Packaging: the fins on a Vehicle Radiator are made of very thin aluminum sheet, often down to 0.2mm thick, and must be fully protected for shipment by carefully packaging the assembly.
- Customer Support: after the purchase, buyers should expect full and readily available support should they have any questions around installation, operation, and troubleshooting concerns, at any time during the long life of the cooler.
Mission-critical vehicles and equipment in over a dozen infrastructure sectors rely on heat transfer components manufactured by Cincinnati Radiator. CR works directly with Original Equipment Manufacturers and Aftermarket service channels to supply premium-grade, long life radiators, coolers, and full cooling packages into extreme applications all over the world. With our expanding inventory and fabrication space at our Fairfield, Ohio facility, we pride ourselves on having a personal touch, ultra-fast lead times, and one-off custom design capabilities.
For your next vehicle or heavy equipment heat transfer project, call us at (513) 874-5555, email us at sarslan@cincyradiator.com, or visit our website at https://cincyradiator.com/